Polymers Turnaround | Kingsport, TN
STARCON International, Inc.
General Contractor > Industrial > Industrial
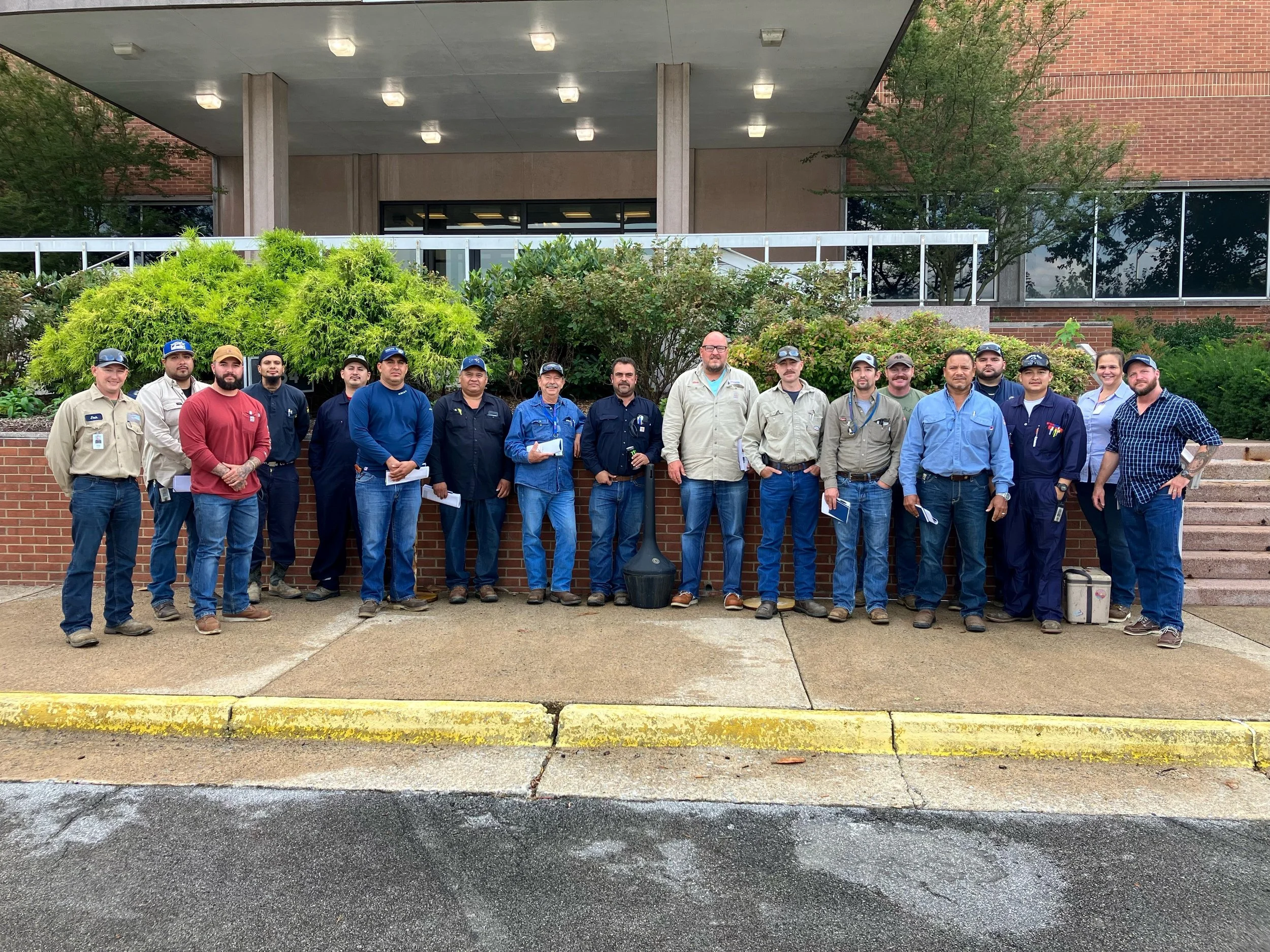







Introduction
The Eastman Chemical Company's Kingsport, Tennessee plant, established in 1920, stands as a cornerstone of the company's global operations. Renowned for producing a diverse array of chemicals, fibers, and specialty materials, this facility plays a pivotal role in various industries, including food and beverage, pharmaceuticals, electronics, and automotive. The Kingsport plant’s significance extends beyond its impressive scale; it serves as a vital hub for Eastman, significantly impacting both the company's trajectory and the regional economy. In 2023, Starcon seized the opportunity to partner with Eastman on the Polymers Turnaround project. Since that initial engagement, we have fostered a continuous presence on-site, quickly establishing ourselves as one of Eastman’s preferred contractors.
Proven Processes Lead to Outstanding Results
The success of the Polymers Turnaround can be attributed to several key factors. Our commitment to a collaborative, partnering approach with Eastman set a solid foundation for the project. Early involvement from all key stakeholders ensured timely issuance of the purchase order and a welldefined work scope.
Starcon implemented a rigorous planning process from inception through completion. Our innovative Risk Mitigation strategy, including our proprietary Readiness Review Process, encompassed a comprehensive site-specific safety plan, quality control measures, staffing logistics, subcontractor management, material oversight, document control, and cost management. This meticulous planning fostered alignment between Eastman and Starcon, facilitating transparency and effective communication.
Starcon mobilized to the site on May 8, 2023, to assist Eastman in the initial planning phases. The project was led by a dedicated team, including Project Manager Jason Smaistrla, Planner/Superintendents Chris Hines, Carlos Caraveo, and Peyton Smith, along with QAQC Supervisor David Hatfield. Our regional leadership—Area Operations Manager Brian Walker, Regional Safety Manager BJ Gual, and Regional QA/QC Manager Chad Gearhart—provided oversight and support throughout the project.
Prior to commencing work, Starcon’s Training & Workforce Development team hosted Front Line Leadership Training, equipping all project managers, superintendents, and frontline leaders with best practices tailored to the project’s unique challenges.
Execution Excellence
Upon mobilization, Starcon’s craft team executed the project with remarkable efficiency, completing 34 exchanger dismantles, 21 vessel and exchanger openings, 118 valve repairs and replacements, and 75 PSV valve replacements. In total, we managed 1,607 flange connections. Throughout the project, we took on an additional 35-40% of discovery work, collaborating effectively with other contractors. Despite these challenges, we delivered the project on schedule and under budget.
HSSE Challenges & Innovations
Starcon navigated significant HSSE challenges, including complex work at heights, heavy equipment operation, and potential hazardous energy releases. Through diligent planning and execution, we achieved a Total Recordable Incident Rate (TRIR) of 0.00 across 45,191 exposure hours, with zero recordable injuries and no dropped objects.
We embraced Eastman’s Goal Zero culture, which resonated with our own safety values. Our innovative team member recognition program prioritized leading indicators, rewarding participation in behavior-based safety, near-miss reporting, and quality of work. Eastman also contributed to this culture of safety through daily recognition for hazard reporting.
QA/QC Innovation
A hallmark of our approach was the development of a customized Quality Control Incident Prevention Plan (QCIPP), aligned with Starcon's Standard Operating Procedures (SOPs). This dynamic plan underwent routine audits and was tailored to meet Eastman's specific standards. Our QA/QC team effectively tracked incidents and maintained a focus on continual improvement, resulting in a project completion rate of 100% flange integrity, zero weld rejections, and a leak-free startup.
Starcon further enhanced quality control by training and certifying inspectors as ASNT-TC-1A Level 2 Dye Penetrant Examiners, allowing us to conduct our own tests and streamline the welding process.
Scheduling & Productivity Innovations
Starcon actively participated in the optimization of project scheduling using Primavera P6, a new software for the Eastman site. Our subject matter experts facilitated its rollout, ensuring a smooth transition and effective measurement of productivity, which was met with client satisfaction.
Celebrating Success
Eastman placed their trust in Starcon for this critical project, a responsibility we honored with our unwavering commitment to excellence. The successful execution of the Polymers Turnaround has solidified our reputation as a top-tier contractor and strengthened our partnership with Eastman. This collaboration has opened doors for future projects, including two major turnarounds scheduled for 2024. In conclusion, the Polymers Turnaround is a testament to the successful partnership between Starcon and Eastman Chemical. Our collective dedication to safety, quality, and operational excellence not only resulted in an on-time and under-budget project but also set the stage for ongoing collaboration that promises to yield further successes. We believe this project exemplifies the essence of excellence in construction, making us a deserving candidate for this prestigious award.