Darlington RNG | Darlington, WI
PDC Electrical Contractors
Specialty Contractor > Electrical: Industrial > Electrical: Industrial


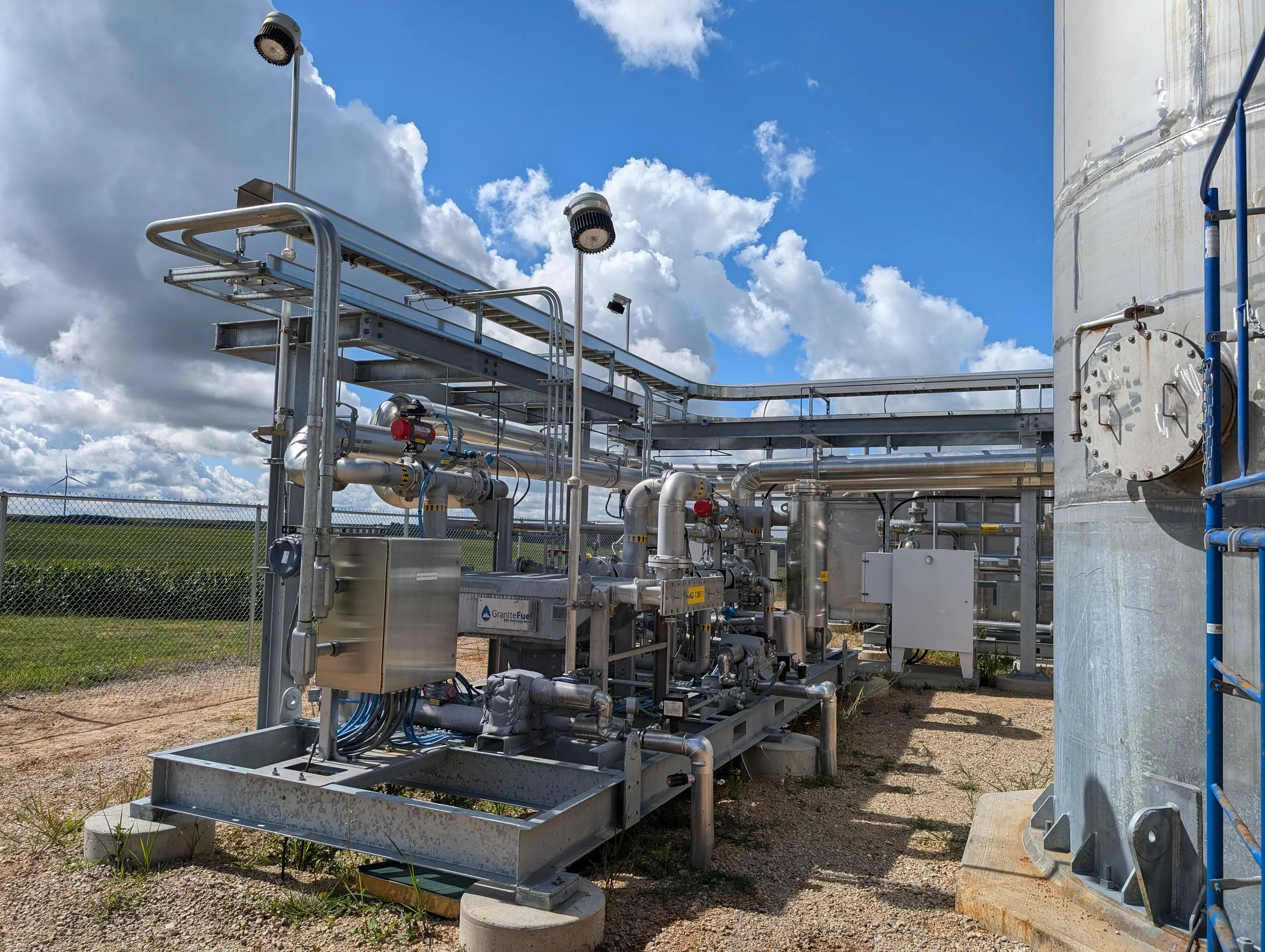

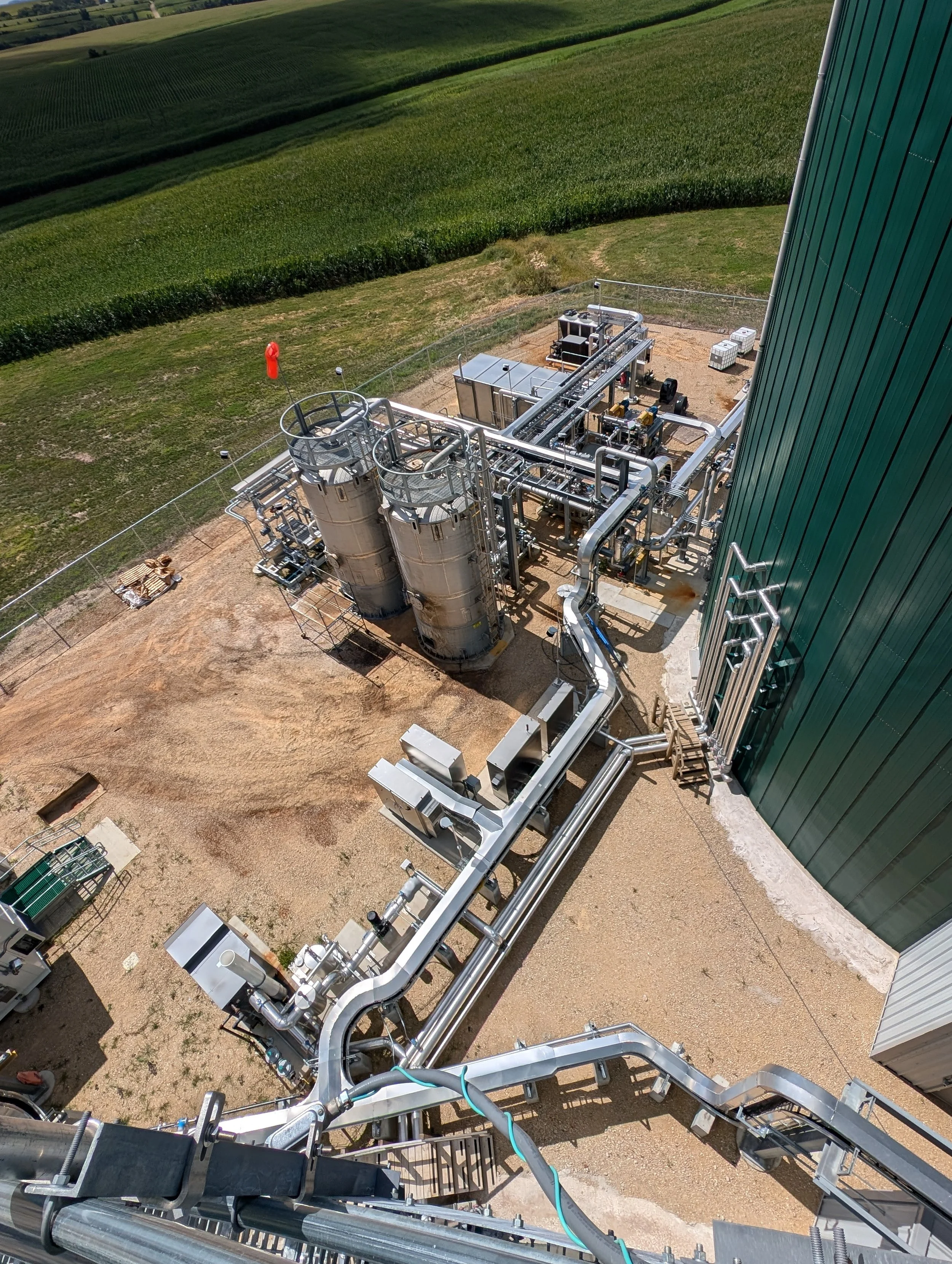
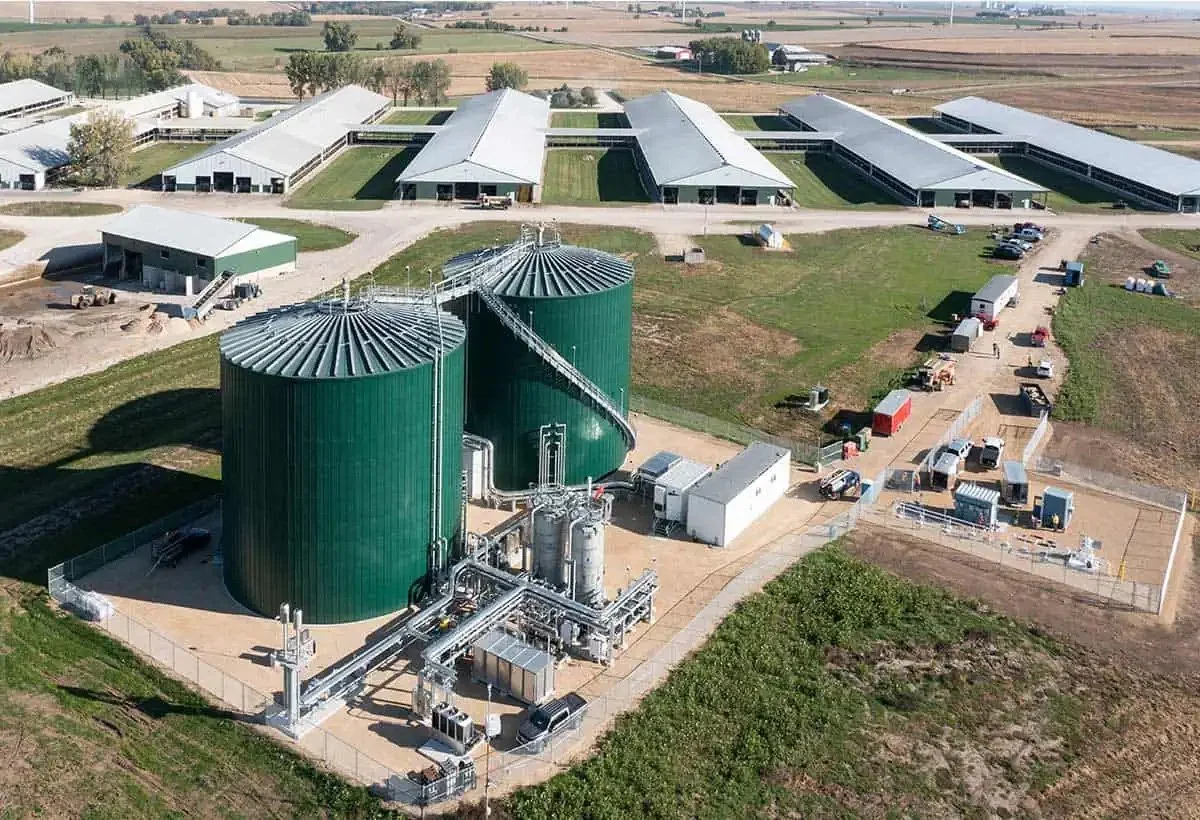
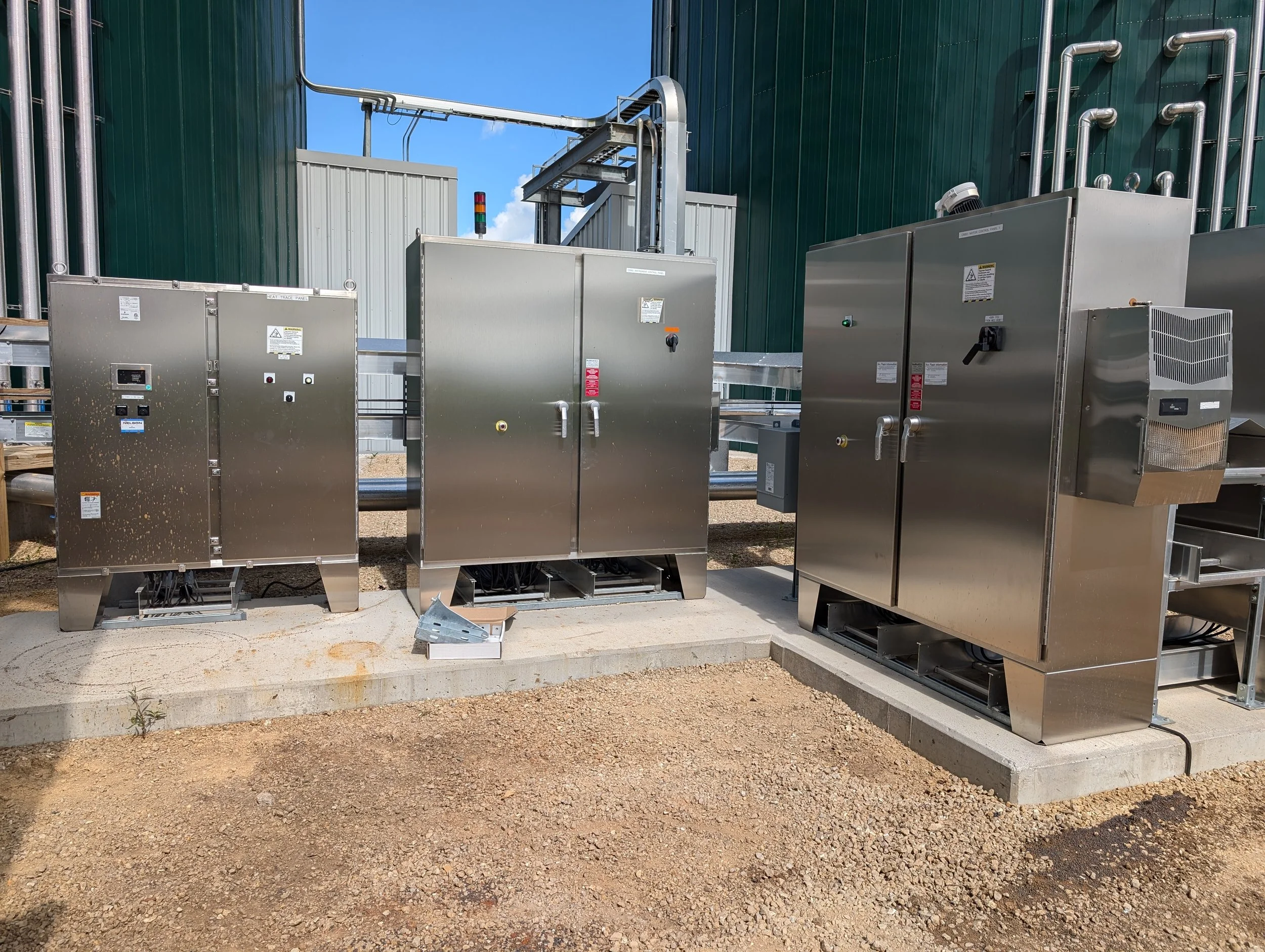
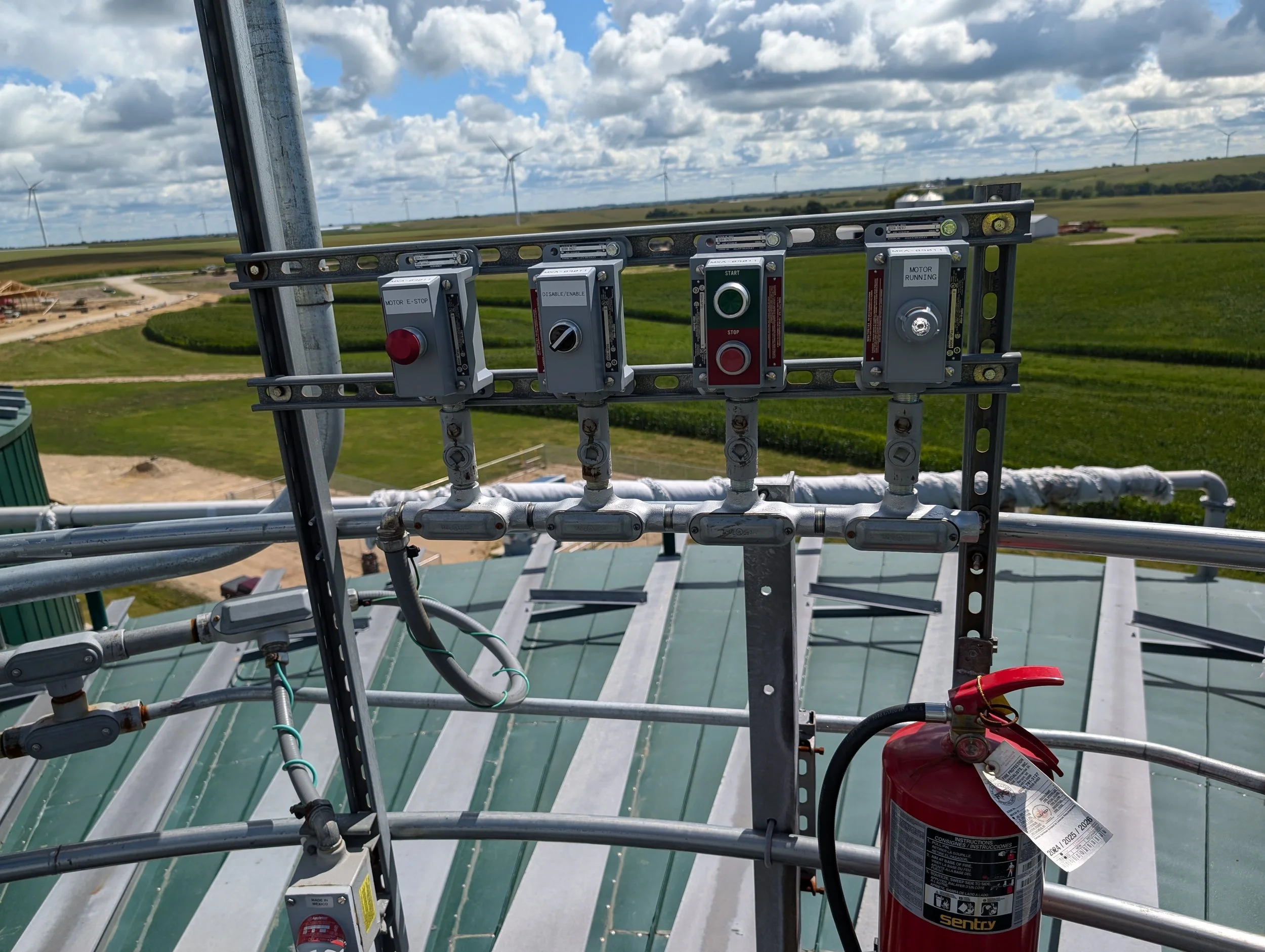


Miron Construction initially approached PDC to work on a renewable natural gas (RNG) facility project in Darlington, Wisconsin. The facility would be the first of its kind in southwestern Wisconsin and would feed back into Alliant Energy’s utility pipeline. PDC gladly accepted this adventure, and then, as they say, the fun began.
PDC had initially estimated the project within their budget, and contracts were signed. However, less than a week after signing the contracts, we encountered our first surprise in this new adventure. We were informed that the project needed to be substantially complete in less than five months. PDC was at least one month from having the site ready and getting materials to start. This left less than four months to complete a project that was estimated to take over 6,000 man-hours. PDC managed to overcome this challenge by strategically scheduling workers, not only on this site but throughout the company, to meet the tight timeline. In the heat of the project, PDC had more than 19 workers on a compact and congested site.
Just like any good adventure, you know there is more than just one surprise lurking around the corner for you. Once on-site, we were involved in many meetings with the general contractor, engineer, owner’s representative, and other contractors on site. These meetings ranged from weekly updates about progress on site, weekly safety meetings, and scheduling meetings. At our first on-site scheduling meeting, PDC was informed that the prefabricated electrical building, supplied by the owner, was not going to arrive on-site until one week before substantial completion. This was a huge setback, and the project manager and superintendent for PDC thought this would now be an impossible task to complete on time. We took the next three days to figure out the path forward on this adventure we were on.
PDC took these unexpected surprises and transformed them into challenges. We pushed ourselves to improve this new path to competition, asked the 19+ onsite personnel to install an electrical system in a way we never have before, and tasked our purchasing staff to adapt to changes in the field. Everyone embraced these challenges, and ultimately, it was very rewarding for all involved.
PDC’s new approach to the completion of building an electrical system for this site with an electric building involved building from the middle towards the end point and the starting point for all electrical and control wiring. The process skids for cleaning and converting methane to natural gas were not available to ship until 2 months before substantial completion. However, the site was finally ready for PDC to start the work, so we began installing our site-wide cable tray system. Our prefab team built 120 supports for the tray system, using over Contracted Scope Darlington RNG Darlington, WI - $1,560,000 1,200 feet of deep slotted strut. Once these arrived on site, they were immediately installed, and the over 1,200 feet of ladder tray was also installed. The cable tray varied in size from 24” down to 12”, with multiple elbows, offsets, rises, and falls for the tray to be a complete system.
Finally, it felt like there was some relief and progress on the site when the tray was completed. As this was coming together, the process skids started showing up and getting set, which was perfect timing for PDC to continue toward completion. We switched gears from installing the cable tray and went right into installing rigid conduit from the tray down to the motors, control panel, and heat trace on each of the skids showing up on site. During the conduit installation, our field crew had to be on top of their game as most of the site was in a classified area. We would have daily discussions on which piece of equipment they were running conduit to on that day or week. We discussed the area they were working in; whether it was classified or not, and if it was a classified area, we confirmed the rating. Once we had that identified, we would then verify if the actual device was factory-sealed or if PDC needed to install a seal-off next to the device. PDC ended up installing 6,150 feet of conduit, over 80 seal-offs in those conduit runs, and using more than 157 classified-rated fittings to complete the conduit runs.
During the project, we collaborated closely with the state inspector. Since this was one of the first projects in the area and the first for PDC, we made the most of our resources by working with the state electrical inspector to address any areas of concern. While he was on site, we had productive discussions about our work and upcoming tasks, and he expressed his admiration for our knowledge of this unusual installation. On one occasion, we discussed a potential issue with one of the skids that had arrived on site. Most of these skids were coming from Canada, which has different electrical code regulations than the United States. Since these skids did not have third-party certification, such as UL, the inspector was responsible for ensuring they met the code. He agreed that the skid in question was not compliant. PDC collaborated with the original manufacturer, general contractor, and engineer to modify the skid to meet the electrical code requirements.
Weekly PDC pushed the supplier to expedite the delivery of the electrical building so we could have as much time as possible. While patiently waiting for the electrical building, we continued with the installation process. We installed four remote panels in the field, strategically placing them just outside the classified area for more practical installation and maintenance in the future. These panels served as a midway point between the electrical building and some of the equipment.
Once wiring was able to start on site, we had our hands full. Not only were we pulling wiring with no destination on one end, but we had over 230,000 feet of wire to pull. Our plan included pulling wiring to each device, motor, or control panel and leaving it coiled up on the electrical building side so we could complete it once the building arrived. There were around 100 wire coils, and we had to ensure they were long enough to reach the correct location in the electrical building. Additionally, they needed to be labeled properly and protected from fading or falling off in the weather, so we wouldn’t have to repull any wiring once the building arrived.
In addition to the motor and control wiring, we had to connect the existing farm’s separation building with the new RNG process by using a fiber optic cable to facilitate communication regarding the amount of product coming into the two large digester tanks. PDC trenched in two 850-foot long 2” PVC conduits and then pulled in a 1,100-foot 24-pair fiber optic cable. To add to the schedule pressure, we had to repair the conduit once and re-pull the fiber optic cable after it was dug up by the fencing contractor three weeks before the project was set to start up.
Two weeks before substantial completion and the start of I/O testing, the electrical building was delivered to the site. Right away, we encountered a final surprise. There was not enough physical space for the service conduits and wiring to come into the building as planned. PDC acted immediately and had a custom box made to fit perfectly between the top of the main breaker and the ceiling. Despite this challenge, we were able to start the motor and control wiring in the building. Our field electricians terminated over 600 wiring terminations in the electrical building itself.
After the electrical building was completed and all wiring was done, we were able to turn on the facility and finish the remaining tasks. We installed heat trace throughout the facility with its own monitoring panel and illuminated end seals on all process piping that required heat trace. These will make it easy for the customer to identify when each line is on, but they also required us to install and connect a few more classified-rated devices. We had to go through the entire cable tray system to ensure that all the cables were properly secured. PDC accomplished this task by using over 7,700 UV-rated zip ties. After confirming that this was done properly, we knew we were making progress towards completion and installed all the covers on the cable tray system. We installed and securely fastened 1,200 feet of peaked cable tray cover.
After completing all the tasks on the job site, from the installation of the first cable tray bracket to the last label, our adventure was coming to an end. Next was the startup and testing phase, the true test of our performance in the eyes of the customer. They had allocated two months for this phase on a project of this size. To our surprise, PDC was able to complete all the startup and I/O testing in just two weeks, thanks to the amazing work of our field crew on site. As a result, the customer was able to start production six weeks earlier than projected, thanks to the work accomplished by PDC.
Overall, PDC was able to complete this project on time for the customer while staying under budget and hours without compromising safety. This project serves as a great example of how everyone in the company rose to the challenge and ensured that the end user received a high-quality, code-compliant, and fully functioning process before they even expected it. Jobs like this make everyone at PDC feel confident that we can tackle any task, even when faced with unexpected surprises. PDC, as a whole, turned these surprises into opportunities, ultimately leading to a highly satisfied customer. A job well done by all!