The Woodlands at Canterfield | West Dundee, IL
McShane Construction Company, LLC
General Contractor > Residential > Residential



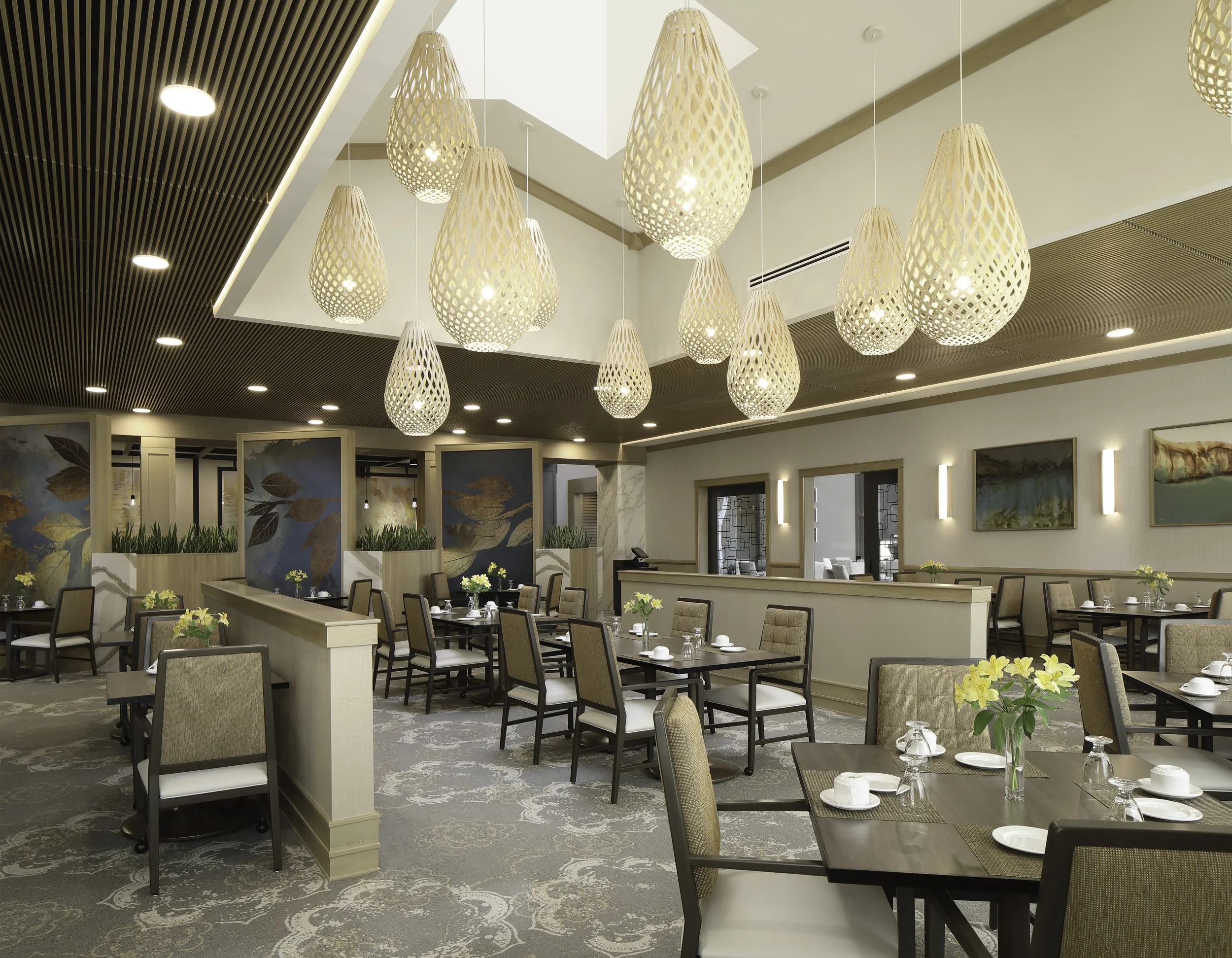

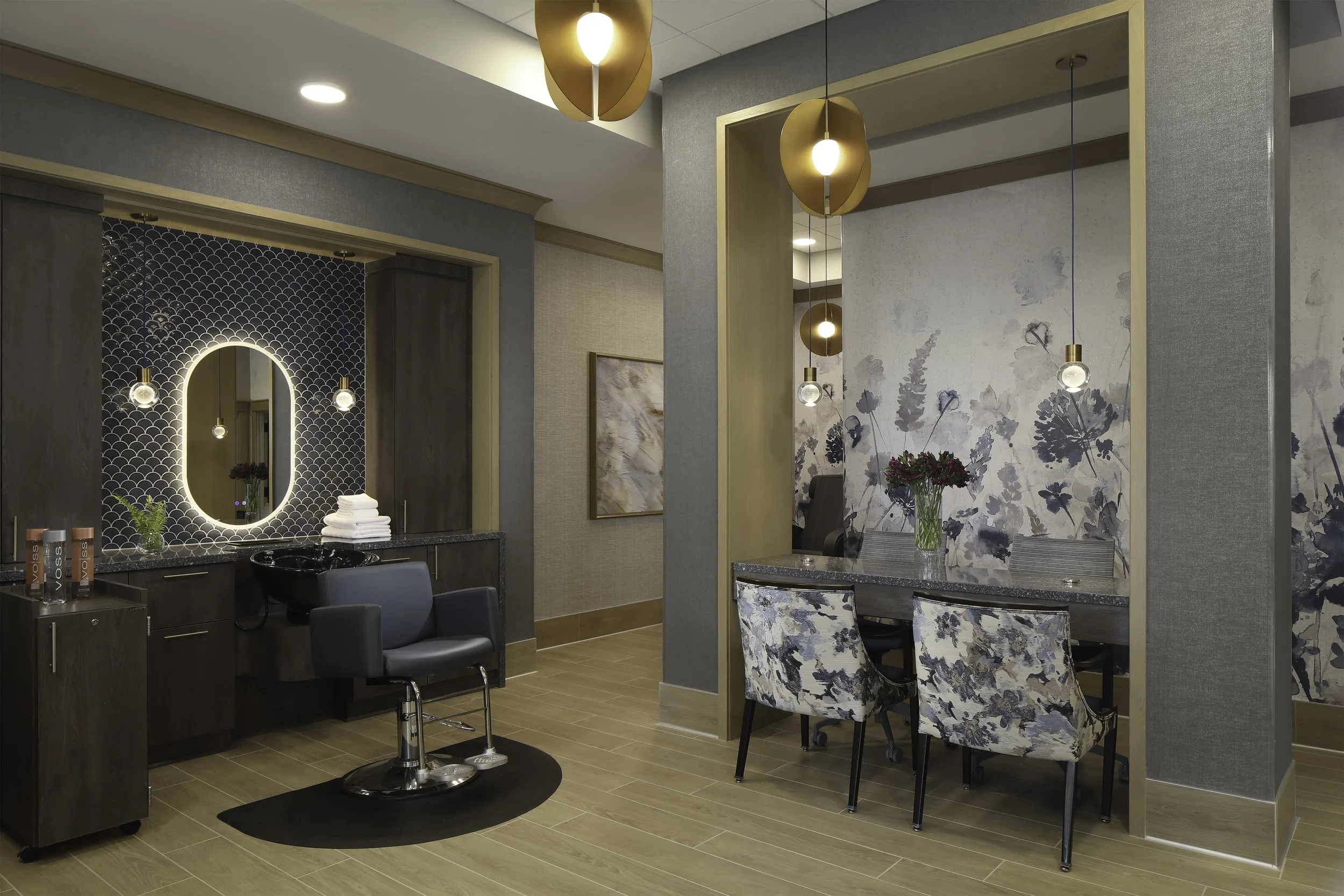
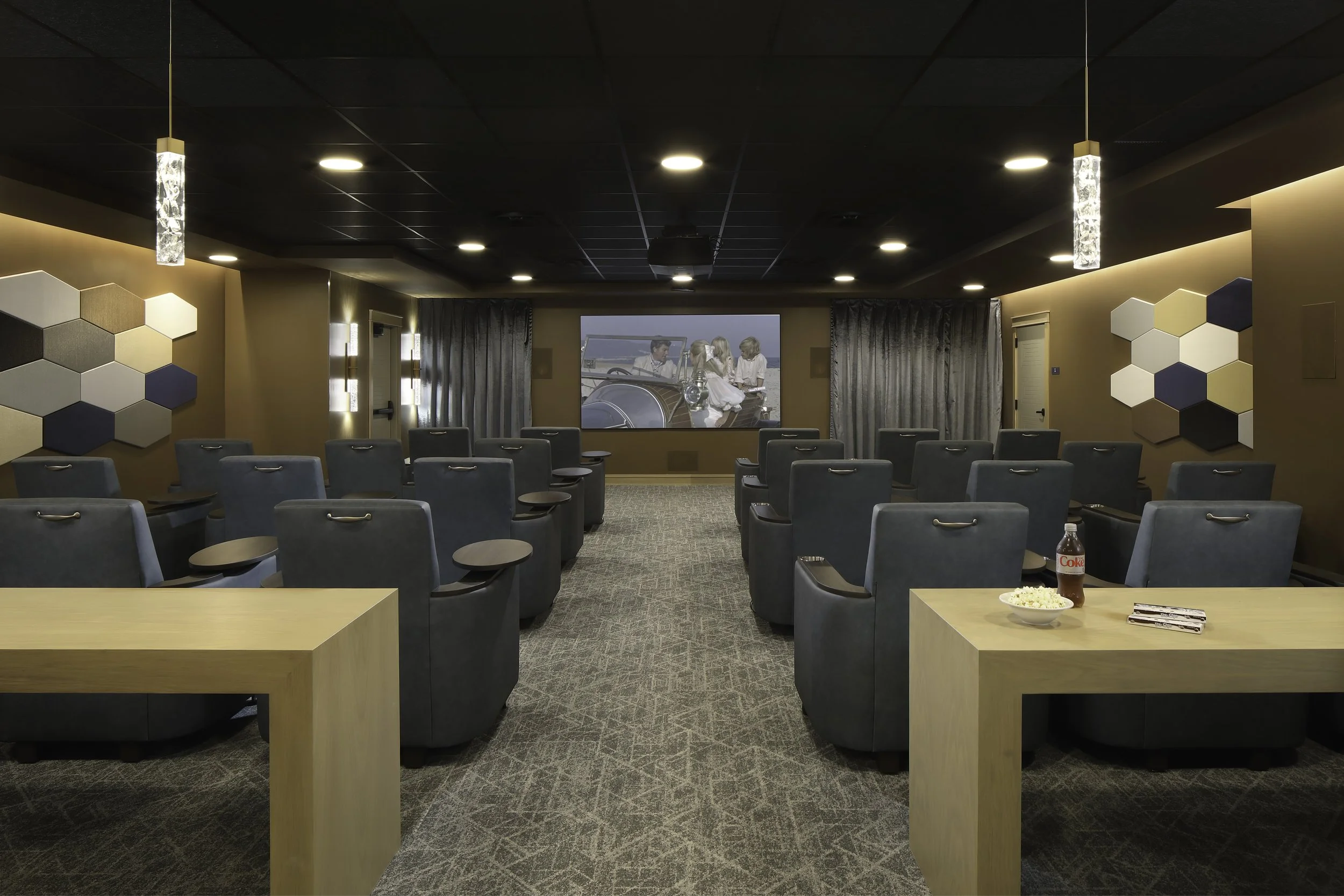

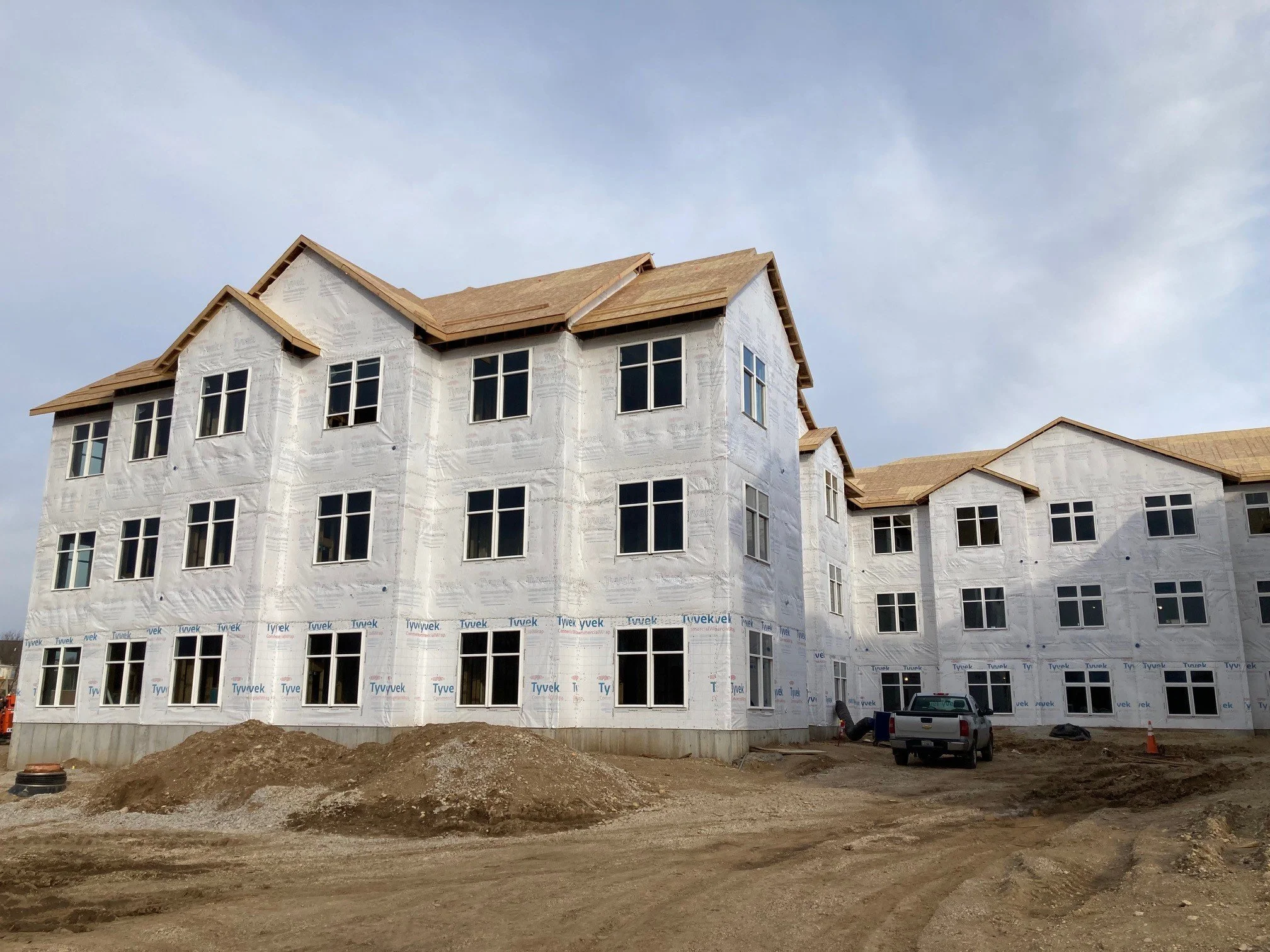

Innovative Programs Relating to Quality Control
Quality in construction begins with complete and fully coordinated design documents. McShane’s Director of Quality Control facilitated this process with the Woodlands at Canterfield project team, including field management staff, by conducting design document reviews to confirm coordination between all design disciplines and to evaluate constructability. McShane also attended meetings with the owner and design consultants with the goal of providing valuable insights into constructability and pricing as it related to design decisions. The McShane Quality Assurance Manual was also an integral component of Woodlands at Canterfield’s construction. Daily/weekly reports on the various construction site conditions and events were recorded using our construction software CMiC. Independent third-party material testing services were conducted on a set schedule in accordance with building codes. Field Observation Reports were prepared for trades to be utilized by field staff and office-based project staff when at the jobsite. Additionally, SALUS, a QA/QC construction software, was used to facilitate QA/QC checklists for the field and project teams to ensure that all work put in place by trades aligned with McShane’s standards for safety and quality procedures. The program is a tool to document quality control as well as a training tool for younger staff to teach them the specific items to monitor for each given trade. As the project neared completion, McShane worked through its closeout procedure by prepunching the building with subcontractors in advance of walking with the owner and architect to minimize the overall list as much as possible. During closeout, the team oversaw the startup and testing of all mechanical and electrical systems and advised the facility’s operating staff on the proper use and maintenance of all systems. McShane also assembled an Operations & Maintenance Manual that was distributed to the owner upon completion and testing of the new facility. These documents included all as-built drawings for each construction discipline and warranty information for all construction materials and equipment that comprised the building.
Innovative Programs Relating to Scheduling
McShane understands that the schedule is the backbone of the project. Field and project management staff are extensively trained in scheduling and collaborating with subcontractors and clients to drive the critical path. The firm has a long-standing track record of meeting tight project schedules for clients and has never been assessed liquidated damages on a project. Throughout the project, McShane created weekly internal schedules. This ensured that all parties involved were aware of the schedule and understood what needed to be accomplished to stay on track.
Value Analysis/Engineering Processes
McShane conducted its Value Engineering analysis during the design phase as part of the preconstruction process. Undertaken concurrently with the building design, each recommendation was identified as a line item with the approximate dollar savings realized by the client. McShane is particularly skilled at assisting the design team in “designing to budget” and presenting wellresearched value engineering options for the project. McShane collaborated with both the owner and the architects to identify cost savings areas without compromising the integrity of the buildings and design.
Special Obstacles Overcome
The Woodlands at Canterfield was the first of a new product type for the developer, and it was also the first time McShane, the developer, and the design teams worked together as a team. The design integrated a variety of high-end finishes, which created unique conditions in nearly every common area. Because the finishes were new to this product type, it was necessary to reevaluate the details and requirements for the rough-in of the building mechanical systems and fire rating requirements, which created challenges for the production schedule. McShane and the design team spent several weeks going room by room through the design intent and working through constructability options to accommodate the mechanical, plumbing, and electrical systems. As a result of this method, the team was able to keep the project within budget without compromising on the highend aesthetics of the space.
Difficulties and Extenuating Circumstances Encountered
The project’s site consisted of large wooded areas and bank run soils along a sloping hill, which created challenges for the construction of the building and reestablishment of new landscaping. The project team worked around the site to remove existing elements, install required foundation and underground utilities, and stabilize regraded soils. As with many projects, The Woodlands at Canterfield faced pandemic-related material shortages and delays. However, when the team encountered these challenges, they worked to find alternative solutions that prevented further delays without compromising quality. For example, with shortages in the lumber market, the team worked with the structural engineers and architects to redesign the structural framing based on products readily available in the sizes required to create the designed aesthetic. COVID, and the restrictions that it brought, impacted the project’s manpower. However, McShane worked quickly and diligently to implement new precautionary parameters. These protocols included six feet social distancing, face coverings, hand washing before entering the construction trailer, isolation of trade crews, temperature checks with contactless thermometers, and virtual or outdoor meetings. This allowed the crews to resume work safely and efficiently.
Innovative Programs Relating to Productivity
McShane has spent the last several years upgrading their technology platforms, thereby increasing efficiency and productivity on their projects. At Woodlands at Canterfield, the firm implemented CMiC, an integrated platform that links the accounting and project management elements for all projects, allowing the project team, owner, subcontractors, and design team to access documents at any time. McShane also implemented SALUS to automate QA/QC inspection. Additionally, PlanGrid was used during the punch list process. This enabled McShane to assign tasks directly to subcontractors during the finishing stages and made it easy for the owner and architect to access punch lists. Together, these platforms enhanced mobility of office personnel, increased productivity of field personnel, cut down on communication time, and improved clarity.